QC7つ道具(Seven basic tools of quality)について
QC7つ道具とは
QCとは
QCはQuality Controlの略であり、品質管理のことを指します。
品質管理では、客観的な指標となる数値データが非常に重要視されており、異常値の検出によって問題を発見して、改善を実施します。
QC7つ道具とは
QC7つ道具は、定量的な数値データの収集や整理、分析を行い、それに基づいて課題を改善する分析手法です。
QC7つ道具の作成手順は「JIS Q 9024:2003 マネジメントシステムのパフォーマンス改善-継続的改善の手順及び技法の指針」で規格化されています。
七つ道具という名前ですが、一般的には「8つの手法」を組み合わせて分析を実施します。
ただし、JIS Q 9024:2003では「層別」手法を取り上げておらず7つの手法となっています。
QC7つ道具の由来
QC7つ道具の考案者や作成時期は不明となっています。
一説には、QCサークル活動(現場で働く従業員たちが、品質管理・品質改善について自主的に話し合い、改善していく活動のこと)の中で発生して、広まったと言われています。
特に、1950年頃から日本科学技術連盟が中心となって、アメリカから統計学者を招聘して、統計手法や品質経営の考え方を日本の産業界に導入しました。
ここから様々な企業や組織でQCサークル活動が生まれており、その中でQC7つ道具が全国的に浸透したようです。
日本の製造業においては、QC7つ道具の手法を早くから取り入れた結果、世界トップクラスの製品品質を実現し、製造業を急成長させたと考えられています。
そのため、現在においても製造業の企業活動では、QC7つ道具が基本的な考え方となっています。
QC7つ道具(8つの手法)
パレート図(Pareto Diagrams)
パレート図とは、データを項目別に集計して多い順に並べた棒グラフと、その累積の構成比を表す折れ線グラフ(累積曲線)によって表した図になります。
この手法は、全体の中で最も大きな影響を与えている要素を明確にして、優先的に対応すべき問題を特定することができます。
【備考】
・パレート図を考案したのは、米国の経営コンサルタントであるJoseph Moses Juranといわれています。
・パレート図は、パレートの法則(80:20の法則)をデータの視点から裏付けるものです。
・パレート図を使うことで、ABC分析(優先順位を判断する分析手法)を実施することができます。
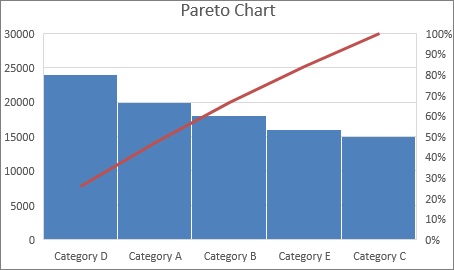
特性要因図(Cause and Effect Diagrams)
特性要因図とは、特性と要因と原因の3つの構成要素を整理することで、因果関係を図式化し、問題を究明する手法です。
特性(effect)とは結果のことであり、要因(Cause)とはその結果をもたらすのに影響を与えた要素のことです。
特性がどのようにしてもたらされたかを可視化することで、そこに潜んでいる問題の「原因」をあぶり出すことができます。
特性要因図は、1950年代に東京大学の教授であった石川馨氏が考案した手法です。
魚の骨図(fishbone diagram)、Ishikawa diagram、CE図とも呼ばれることもあります。
魚の骨図というのは、特性と要因の関係を系統的に線で結んだ図が、まるで魚の骨のように見えるためです。
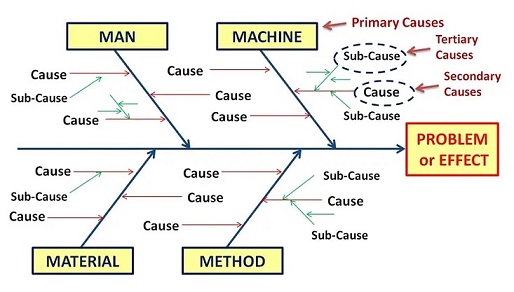
グラフ(Graphs)
グラフとは、データを視覚的に表現した図であり、数値の比較や変化を直感的に把握するために使用します。
品質管理によく使われるグラフとしては、以下の5種類があります。
- 折れ線グラフ(変動を見る)
- 棒グラフ(数量などを比較する)
- 円グラフ(比率を見る)
- 帯グラフ(比率を比較する)
- レーダーチャート(バランスを見る)
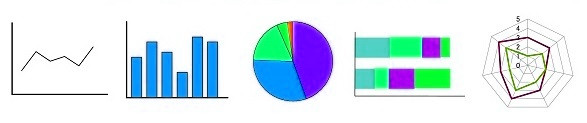
管理図(Control Chart)
管理図とは、中央線(平均値を示す管理線)と上下一対の管理限界線を引いて、折れ線グラフで測定値の変化を見る手法です。
例えば、製品などの特性値をプロットし、品質不良や製造工程の異常を検出して不良原因の除去や再発防止に役立てることができます。
プロジェクトの品質マネジメントにおいても、プロセスが安定しているかどうか、又はパフォーマンスが予測のとおりであるかを判断するために用いることができます。
管理図は、1924年にアメリカの統計学者シューハート氏(W. A. Shewhart)が考案した手法です。
そのため、シューハート管理図とも呼ばれています。
管理図は目的別に多くの手法が考案されており、計量管理図や計数管理図、希少管理図などがあります。
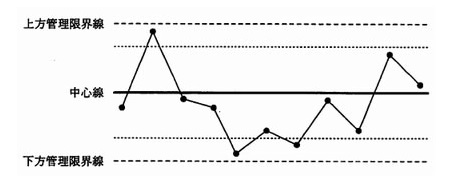
チェックシート(Check Sheets)
チェックシートとは、点検や確認、現状の調査を目的に作成された調査表のことです。
事前に作成しておいた項目に沿って結果を記載することで、客観性のある事実を記録できます。
チェックシートは、調査用と点検用の2種類あります。
調査用チェックシートは、問題解決において必要となるデータの収集が主な目的です。
点検用チェックシートは、項目の通りに点検することで、事故や間違いの防止、安全の確保を実現します。
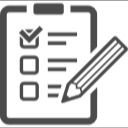
ヒストグラム(Histogram)
ヒストグラムとは、縦軸に度数、横軸に階級をとり、連続データの分布を表す柱状グラフのことです。
ヒストグラムはデータの分布を可視化する手法であり、データの偏りやばらつきを分析するために利用します。
柱図表、度数分布図、柱状グラフとも呼ばれます。
ヒストグラムは順序がある項目、つまり、連続性のあるデータに対して有効な手法です。
連続性とは例えば、身長165cm以上170cm未満、170cm以上175cm未満、175cm以上180cm未満といった連続した分類項目のことです。
連続性がないデータの場合、正しい分布の解析ができなくなるので注意が必要です。
また、ヒストグラムは、階級の幅や階級の数を変更するとグラフの形が大きく変わってしまうので、条件定義の扱いについても注意が必要です。
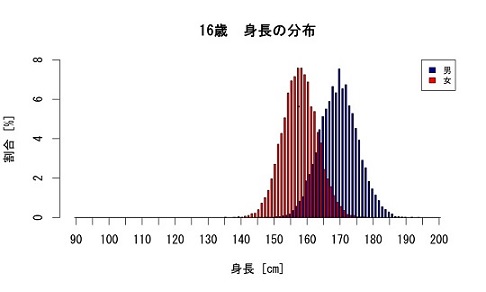
散布図(Scatter Diagrams)
散布図とは、二つの要素を縦軸、横軸として各データを表記し、データの関係性を分析する図のことです。
例えば、プログラムの規模が大きくなるにつれてバグの摘出数が増えた場合に、この2つの要素がどのような関係なのか分析するために利用します。
点を散らしたように見えるため、散布図と呼ばれます。
散布図に現れるパターンは、大きく分けて「正の相関関係」「負の相関関係」「相関がない」の3種類があります。
正の相関とは、あるデータの値が高ければ高いほど、もう一方のデータの値が高くなる傾向がある関係のことです。
負の相関とは、あるデータの値が高ければ高いほど、もう一方のデータの値が低くなる傾向がある関係のことです。
相関がないとは、片方の要素にもう片方の要素が関係しない関係のことです。
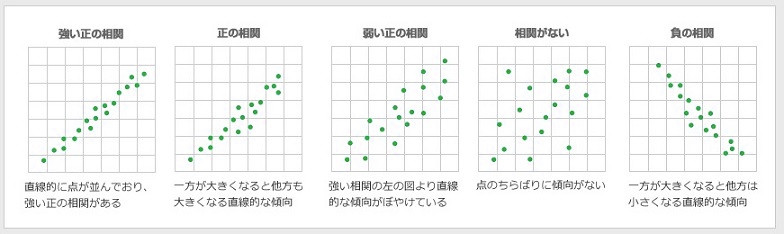
層別(Stratification)について
層別とは、得られたデータを特徴ごとにグループ化し、分類したグループごとに分析する手法です。
データの共通点や特徴に着目して分類することで、複雑な事柄を解きほぐし問題点を具体化することができます。
例えば、ある製品の品質に注目した場合、原料、機械、ひと、時間などの要素に注目してグループ分けします。
そして分類したグループ毎に、製造プロセスのどこに品質低下の要因があるか検討します。
検討した結果、層別に選んだ要素に問題の原因が見つからなければ、別の層別要素を切り口にして検討します。
層別 | 各要因 |
---|---|
人で分ける | 経験年数別、年齢別、男女別、作業班別など |
機械で分ける | 加工方法別、装置別、工程別、型式別、ライン別など |
原材料で分ける | メーカー別、ロット別、サイズ別、産地別、購入時期別など |
環境で分ける | 気温、湿度、天候、雨期∕乾期など |
層別は、日本科学技術連盟ではQC7つ道具として定義されていますが、
「JIS Q 9024:2003」(マネジメントシステムのパフォーマンス改善)には取り入れられてはいません。
また、層別をQC7つ道具に含めないと説明しているWebサイトも多数あります。
しかしながら、層別はQC7つ道具の他の手法と組み合わせて用いることができ、それが非常に効果的であることは間違いありません。